Destylator przemysłowy to urządzenie służące do separacji składników cieczy na podstawie różnicy ich temperatur wrzenia. Proces ten jest kluczowy w wielu gałęziach przemysłu, takich jak chemiczny, petrochemiczny czy spożywczy. Destylacja polega na podgrzewaniu cieczy do momentu, w którym jej składniki zaczynają parować, a następnie schładzaniu pary, aby uzyskać czystą substancję w postaci cieczy. W przemyśle stosuje się różne typy destylatorów, w tym destylatory prostokątne, kolumnowe oraz frakcyjne. Każdy z tych typów ma swoje unikalne zastosowania i zalety. Na przykład, destylatory kolumnowe są często wykorzystywane do separacji wielu składników jednocześnie, co czyni je bardziej efektywnymi w produkcji dużych ilości substancji chemicznych. Warto również zauważyć, że proces destylacji może być przeprowadzany w różnych warunkach ciśnienia, co wpływa na temperatury wrzenia i efektywność separacji.
Jakie są główne zastosowania destylatorów przemysłowych
Destylatory przemysłowe mają szerokie zastosowanie w różnych branżach, co czyni je niezwykle ważnym elementem nowoczesnej produkcji. W przemyśle chemicznym są one wykorzystywane do oczyszczania surowców oraz produkcji chemikaliów o wysokiej czystości. Na przykład, w procesie produkcji alkoholu etylowego destylatory pozwalają na oddzielenie etanolu od wody i innych zanieczyszczeń. W przemyśle petrochemicznym destylatory służą do rozdzielania ropy naftowej na różne frakcje, takie jak benzyna, olej napędowy czy nafta. Każda z tych frakcji ma swoje specyficzne zastosowania, co sprawia, że proces destylacji jest kluczowy dla wydobycia i przetwarzania surowców energetycznych. Ponadto, destylatory znajdują zastosowanie w produkcji olejków eterycznych z roślin, gdzie pozwalają na wydobycie cennych substancji zapachowych i terapeutycznych. W przemyśle spożywczym destylacja jest wykorzystywana do produkcji napojów alkoholowych oraz ekstraktów smakowych.
Jakie są różnice między destylatorami przemysłowymi a laboratoryjnymi
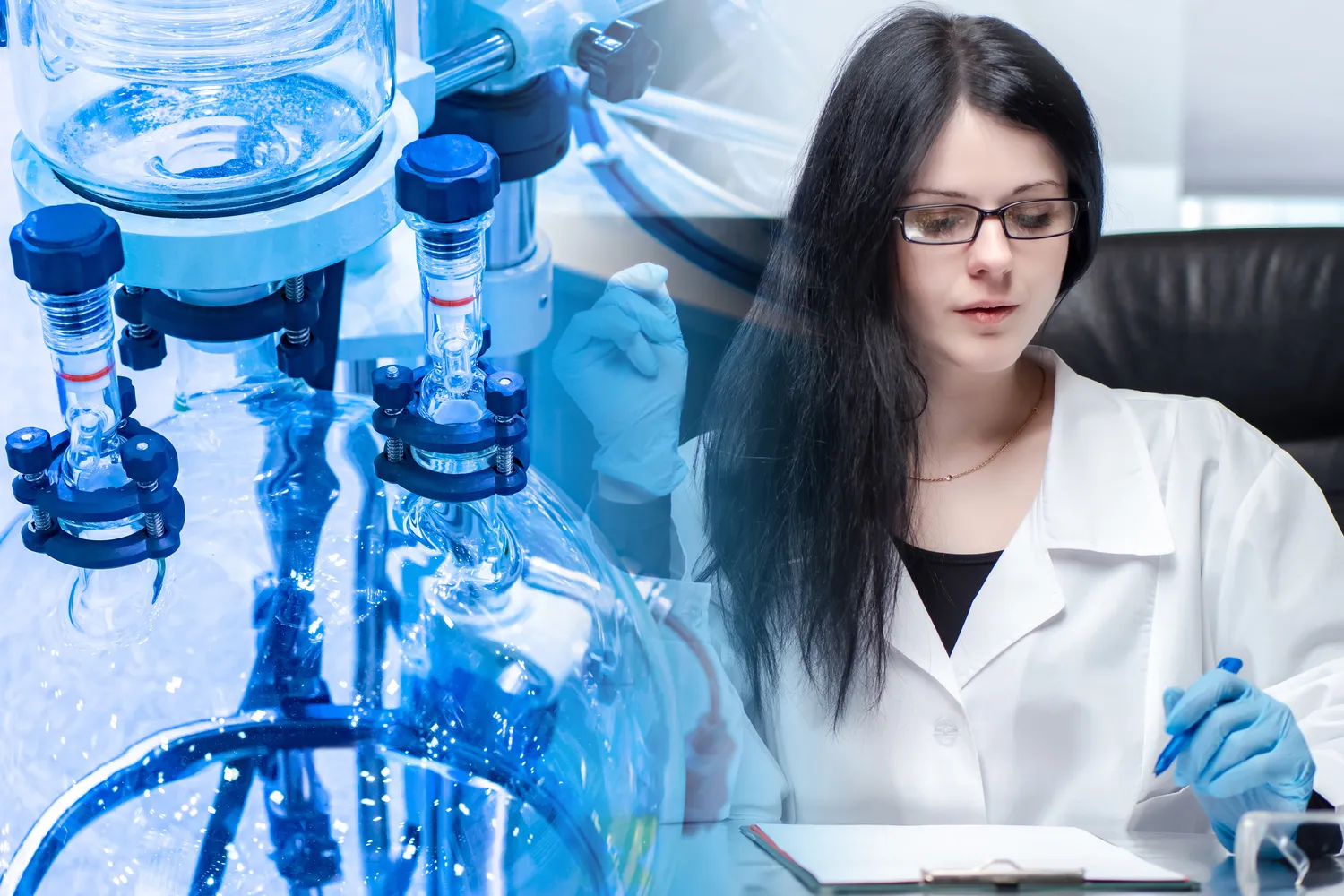
Destylatory przemysłowe i laboratoryjne różnią się przede wszystkim skalą oraz przeznaczeniem. Destylatory przemysłowe są zaprojektowane do pracy na dużą skalę i są zdolne do przetwarzania znacznych ilości cieczy w krótkim czasie. Zazwyczaj charakteryzują się one bardziej zaawansowanymi systemami automatyzacji oraz kontrolą procesów, co pozwala na optymalizację wydajności i jakości produktu końcowego. Z kolei destylatory laboratoryjne są zazwyczaj mniejsze i służą do przeprowadzania eksperymentów oraz badań naukowych. Ich konstrukcja umożliwia łatwiejsze monitorowanie i kontrolowanie poszczególnych parametrów procesu destylacji. W laboratoriach często wykorzystuje się prostsze modele destylatorów, które pozwalają na precyzyjne oddzielanie składników przy mniejszych ilościach materiału. Różnice te wpływają również na koszty eksploatacji oraz wymagania dotyczące konserwacji urządzeń. W przypadku destylatorów przemysłowych konieczne jest zapewnienie odpowiednich warunków pracy oraz regularna konserwacja ze względu na intensywność użytkowania.
Jakie technologie wspierają nowoczesne destylatory przemysłowe
Nowoczesne destylatory przemysłowe korzystają z zaawansowanych technologii, które zwiększają ich efektywność oraz bezpieczeństwo pracy. Jednym z najważniejszych trendów jest automatyzacja procesów, która pozwala na zdalne monitorowanie i kontrolowanie parametrów pracy urządzenia. Dzięki zastosowaniu systemów informatycznych możliwe jest zbieranie danych o wydajności oraz jakości produktów w czasie rzeczywistym, co ułatwia podejmowanie decyzji operacyjnych. Kolejnym istotnym aspektem jest wykorzystanie technologii odzysku ciepła, która pozwala na zmniejszenie zużycia energii podczas procesu destylacji. Systemy te umożliwiają ponowne wykorzystanie ciepła generowanego podczas parowania cieczy, co przekłada się na niższe koszty eksploatacyjne oraz mniejszy wpływ na środowisko naturalne. Dodatkowo nowoczesne destylatory często wyposażone są w zaawansowane systemy filtracji oraz oczyszczania gazów odlotowych, co przyczynia się do poprawy jakości powietrza wokół zakładów przemysłowych.
Jakie są kluczowe elementy konstrukcyjne destylatorów przemysłowych
Destylatory przemysłowe składają się z wielu kluczowych elementów, które współpracują ze sobą, aby zapewnić efektywny proces separacji składników cieczy. Podstawowym elementem jest zbiornik do podgrzewania, w którym umieszczana jest ciecz do destylacji. Zbiornik ten jest zazwyczaj wyposażony w system grzewczy, który może działać na różne sposoby, takie jak elektryczność, para wodna czy olej termalny. Kolejnym istotnym elementem jest kolumna destylacyjna, która umożliwia separację składników na podstawie różnicy ich temperatur wrzenia. W kolumnach frakcyjnych znajdują się różne elementy, takie jak złoża, które wspomagają proces kondensacji i parowania. Po przejściu przez kolumnę, para trafia do skraplacza, gdzie zostaje schłodzona i przekształcona w ciecz. Skraplacze mogą być chłodzone wodą lub powietrzem, w zależności od wymagań procesu. Oprócz tych podstawowych komponentów, nowoczesne destylatory często zawierają dodatkowe urządzenia kontrolne i monitorujące, które pozwalają na precyzyjne zarządzanie parametrami procesu oraz zapewniają bezpieczeństwo pracy.
Jakie są wyzwania związane z eksploatacją destylatorów przemysłowych
Eksploatacja destylatorów przemysłowych wiąże się z wieloma wyzwaniami, które mogą wpływać na efektywność procesów oraz bezpieczeństwo pracy. Jednym z głównych problemów jest konieczność regularnej konserwacji urządzeń, aby zapobiec awariom oraz utrzymaniu ich w dobrym stanie technicznym. Z czasem w kolumnach destylacyjnych mogą gromadzić się osady oraz zanieczyszczenia, co prowadzi do obniżenia wydajności procesu. Dlatego regularne czyszczenie i inspekcje są niezbędne. Innym wyzwaniem jest zarządzanie zużyciem energii oraz surowców. W obliczu rosnących kosztów energii i surowców wiele firm stara się optymalizować swoje procesy produkcyjne w celu zwiększenia efektywności energetycznej. Wprowadzenie technologii odzysku ciepła oraz automatyzacji procesów może znacząco pomóc w tym zakresie. Dodatkowo należy zwrócić uwagę na kwestie związane z ochroną środowiska oraz zgodnością z regulacjami prawnymi dotyczącymi emisji gazów i odpadów.
Jakie są przyszłe kierunki rozwoju technologii destylacji przemysłowej
Przyszłość technologii destylacji przemysłowej wydaje się być obiecująca dzięki ciągłemu rozwojowi innowacyjnych rozwiązań technologicznych. Jednym z najważniejszych kierunków jest dalsza automatyzacja procesów produkcyjnych. Dzięki zastosowaniu sztucznej inteligencji i zaawansowanych algorytmów analizy danych możliwe będzie jeszcze dokładniejsze monitorowanie i optymalizacja parametrów pracy destylatorów. Automatyczne systemy będą mogły dostosowywać warunki pracy w czasie rzeczywistym, co przyczyni się do zwiększenia wydajności oraz jakości produktów końcowych. Kolejnym ważnym trendem jest rozwój technologii odzysku ciepła i energii, co pozwoli na zmniejszenie kosztów eksploatacyjnych oraz ograniczenie wpływu na środowisko naturalne. W miarę jak rośnie świadomość ekologiczna społeczeństwa oraz regulacje dotyczące ochrony środowiska stają się coraz bardziej rygorystyczne, firmy będą musiały inwestować w technologie przyjazne dla środowiska. Dodatkowo rozwój materiałów o lepszych właściwościach termicznych może przyczynić się do poprawy efektywności procesów destylacyjnych.
Jakie są koszty związane z zakupem i eksploatacją destylatorów przemysłowych
Koszty związane z zakupem i eksploatacją destylatorów przemysłowych mogą być znaczne i zależą od wielu czynników, takich jak typ urządzenia, jego wydajność oraz zastosowane technologie. Zakup nowoczesnego destylatora to często duża inwestycja początkowa, która może wynosić od kilku tysięcy do nawet milionów złotych w przypadku dużych instalacji przemysłowych. Koszty te obejmują nie tylko sam sprzęt, ale także instalację oraz uruchomienie urządzenia. Ponadto należy uwzględnić koszty związane z konserwacją i serwisowaniem urządzeń, które są niezbędne dla utrzymania ich w dobrym stanie technicznym oraz zapewnienia efektywności pracy. Koszty eksploatacyjne obejmują również zużycie energii elektrycznej lub innych źródeł ciepła potrzebnych do podgrzewania cieczy oraz koszty surowców wykorzystywanych w procesie destylacji. Warto również pamiętać o kosztach związanych z przestrzeganiem regulacji dotyczących ochrony środowiska oraz ewentualnymi karami za ich naruszenie.
Jakie są najczęściej stosowane materiały w budowie destylatorów przemysłowych
W budowie destylatorów przemysłowych wykorzystuje się różnorodne materiały, które mają kluczowe znaczenie dla trwałości i efektywności urządzeń. Najczęściej stosowanym materiałem jest stal nierdzewna, która charakteryzuje się wysoką odpornością na korozję oraz wysokimi temperaturami. Dzięki tym właściwościom stal nierdzewna jest idealnym materiałem do budowy zbiorników, kolumn destylacyjnych oraz skraplaczy. W przypadku niektórych aplikacji mogą być również używane materiały kompozytowe lub tworzywa sztuczne odporne na działanie chemikaliów. Ważnym aspektem jest także wybór odpowiednich uszczelek i elementów łączących, które muszą być odporne na wysokie temperatury oraz agresywne substancje chemiczne występujące podczas procesu destylacji. Dodatkowo niektóre komponenty mogą być pokrywane specjalnymi powłokami ochronnymi w celu zwiększenia ich trwałości i odporności na działanie substancji chemicznych.
Jakie są różnice między różnymi typami destylatorów przemysłowych
Różne typy destylatorów przemysłowych różnią się między sobą konstrukcją, zasadą działania oraz zastosowaniami w przemyśle. Destylatory prostokątne to jedne z najprostszych modeli, które znajdują zastosowanie głównie w małych zakładach produkcyjnych lub laboratoriach. Charakteryzują się one prostą budową i łatwością obsługi, jednak ich wydajność może być ograniczona w porównaniu do bardziej zaawansowanych modeli. Destylatory kolumnowe to bardziej skomplikowane urządzenia, które umożliwiają separację wielu składników jednocześnie dzięki zastosowaniu kolumn frakcyjnych. Są one powszechnie stosowane w przemyśle petrochemicznym oraz chemicznym do produkcji różnych frakcji cieczy o wysokiej czystości. Kolejnym typem są destylatory próżniowe, które działają w obniżonym ciśnieniu atmosferycznym, co pozwala na obniżenie temperatur wrzenia substancji i minimalizację degradacji termicznej składników wrażliwych na wysokie temperatury.