Aby skutecznie połączyć dwa kompresory, należy przede wszystkim zrozumieć ich działanie oraz odpowiednio zaplanować cały proces. Na początku warto zwrócić uwagę na typy kompresorów, które zamierzamy połączyć. Istotne jest, aby oba urządzenia miały podobne parametry techniczne, takie jak ciśnienie robocze oraz wydajność. W przeciwnym razie może dojść do nieprawidłowego działania systemu. Kolejnym krokiem jest przygotowanie odpowiednich narzędzi i materiałów, takich jak rury, złączki oraz zawory. Ważne jest również, aby upewnić się, że wszystkie elementy są kompatybilne z używanymi kompresorami. Po zebraniu wszystkich niezbędnych komponentów można przystąpić do montażu. Należy pamiętać o zachowaniu odpowiednich zasad bezpieczeństwa podczas pracy z urządzeniami pneumatycznymi.
Jakie materiały i narzędzia będą potrzebne do połączenia kompresorów?
Przygotowanie odpowiednich materiałów i narzędzi jest kluczowe dla sukcesu projektu łączenia dwóch kompresorów. Na początek warto zaopatrzyć się w rury o odpowiedniej średnicy, które będą służyć do połączenia obu urządzeń. Rury powinny być wykonane z materiałów odpornych na wysokie ciśnienie oraz korozję, co zapewni ich długotrwałe użytkowanie. Dodatkowo niezbędne będą złączki i zawory, które umożliwią prawidłowe połączenie oraz kontrolę przepływu powietrza. Warto również mieć pod ręką uszczelki, które zapobiegną wyciekom powietrza w miejscach połączeń. Jeśli chodzi o narzędzia, to przyda się klucz płaski lub nasadowy do dokręcania złączek oraz wkrętarka do montażu elementów konstrukcyjnych. Warto także mieć na wyposażeniu manometr, który pozwoli na monitorowanie ciśnienia w systemie.
Jakie są najczęstsze błędy przy łączeniu kompresorów?
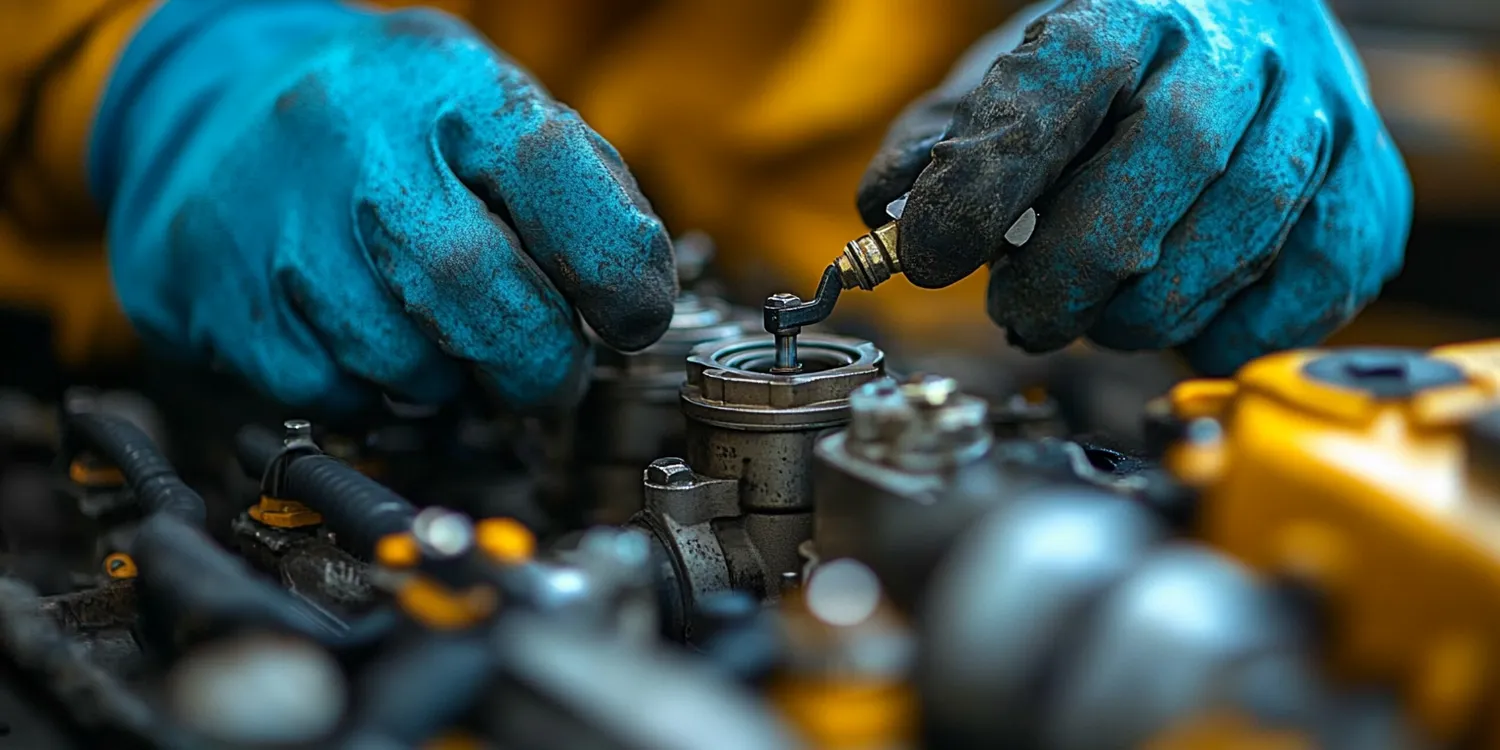
Podczas łączenia dwóch kompresorów istnieje wiele pułapek, które mogą prowadzić do problemów z działaniem całego systemu. Jednym z najczęstszych błędów jest niewłaściwe dobranie parametrów technicznych obu urządzeń. Jeśli jeden z kompresorów ma znacznie wyższą wydajność niż drugi, może to prowadzić do nadmiernego obciążenia słabszego urządzenia i jego szybszego zużycia. Innym powszechnym błędem jest nieodpowiednie uszczelnienie połączeń, co skutkuje wyciekami powietrza i obniżeniem efektywności całego systemu. Należy również zwrócić uwagę na prawidłowy montaż zaworów i złączek, ponieważ ich niewłaściwe umiejscowienie może prowadzić do problemów z ciśnieniem roboczym. Często zdarza się także ignorowanie zasad bezpieczeństwa, co może prowadzić do groźnych sytuacji podczas pracy z urządzeniami pneumatycznymi.
Jakie korzyści płyną z połączenia dwóch kompresorów?
Łączenie dwóch kompresorów niesie ze sobą wiele korzyści, które mogą znacząco wpłynąć na efektywność pracy w różnych branżach. Przede wszystkim zwiększa to wydajność całego systemu pneumatycznego, co pozwala na szybsze wykonywanie prac wymagających dużych ilości sprężonego powietrza. Dzięki połączeniu dwóch kompresorów można uzyskać stabilniejsze ciśnienie robocze, co przekłada się na lepszą jakość wykonywanych zadań. Dodatkowo posiadanie dwóch urządzeń umożliwia elastyczne zarządzanie pracą – w przypadku awarii jednego z nich drugie może przejąć jego funkcje, co minimalizuje przestoje w produkcji czy innych procesach wymagających sprężonego powietrza. Połączenie kompresorów może również przyczynić się do oszczędności energii – nowoczesne modele są często bardziej efektywne energetycznie niż starsze wersje, co przekłada się na niższe rachunki za prąd.
Jakie są różnice między różnymi typami kompresorów?
Wybór odpowiedniego typu kompresora jest kluczowy dla efektywności całego systemu. Na rynku dostępne są różne rodzaje kompresorów, a ich działanie opiera się na różnych zasadach. Kompresory tłokowe, na przykład, działają na zasadzie zmniejszania objętości powietrza w cylindrze, co prowadzi do jego sprężania. Są one często stosowane w małych warsztatach i do prostych aplikacji, ale mogą być głośne i mniej efektywne przy dłuższym użytkowaniu. Z kolei kompresory śrubowe charakteryzują się wyższą wydajnością i cichszą pracą, co czyni je idealnym rozwiązaniem dla przemysłu. Działają na zasadzie sprężania powietrza za pomocą wirujących śrub, co pozwala na uzyskanie stabilnego ciśnienia roboczego. Innym typem są kompresory spiralne, które również oferują wysoką wydajność i niski poziom hałasu, ale są zazwyczaj droższe w zakupie. Warto również zwrócić uwagę na kompresory bezolejowe, które eliminują ryzyko zanieczyszczenia sprężonego powietrza olejem, co jest istotne w branżach wymagających czystości, takich jak medycyna czy spożywczy przemysł.
Jakie są najlepsze praktyki przy łączeniu kompresorów?
Aby zapewnić prawidłowe działanie połączonych kompresorów, warto przestrzegać kilku najlepszych praktyk. Po pierwsze, przed przystąpieniem do montażu należy dokładnie zaplanować cały proces oraz sporządzić schemat instalacji. Dzięki temu unikniemy niepotrzebnych błędów i zaoszczędzimy czas podczas pracy. Ważne jest również, aby przed połączeniem urządzeń przeprowadzić ich dokładną inspekcję techniczną. Upewnijmy się, że oba kompresory są sprawne i nie mają żadnych uszkodzeń mechanicznych ani wycieków powietrza. Kolejnym krokiem jest odpowiednie przygotowanie miejsca pracy – powinno być ono dobrze wentylowane oraz wolne od zbędnych przedmiotów, które mogą utrudniać dostęp do urządzeń. Podczas montażu należy stosować odpowiednie narzędzia oraz materiały zgodne z zaleceniami producenta. Po zakończeniu instalacji warto przeprowadzić testy funkcjonalne, aby upewnić się, że system działa prawidłowo i osiąga wymagane parametry ciśnienia oraz wydajności.
Jakie są koszty związane z połączeniem dwóch kompresorów?
Koszty związane z połączeniem dwóch kompresorów mogą się znacznie różnić w zależności od wielu czynników. Przede wszystkim należy uwzględnić cenę samych urządzeń – jeśli już posiadamy jeden z nich, koszt zakupu drugiego będzie kluczowym elementem budżetu. Dodatkowo trzeba doliczyć wydatki na materiały potrzebne do instalacji, takie jak rury, złączki czy zawory. Koszt tych komponentów może się różnić w zależności od ich jakości oraz producenta. Warto również uwzględnić ewentualne koszty wynajęcia specjalisty do montażu, jeśli nie czujemy się na siłach przeprowadzić tej operacji samodzielnie. Czasami konieczne może być także dostosowanie istniejącej infrastruktury pneumatycznej do nowych warunków pracy, co wiąże się z dodatkowymi wydatkami. Należy pamiętać o kosztach eksploatacyjnych związanych z użytkowaniem dwóch kompresorów – większa moc systemu może prowadzić do wyższych rachunków za energię elektryczną.
Jakie są najczęstsze pytania dotyczące łączenia kompresorów?
Wiele osób zastanawia się nad kwestiami związanymi z łączeniem kompresorów i ma wiele pytań dotyczących tego procesu. Jednym z najczęściej zadawanych pytań jest to, czy można łączyć różne typy kompresorów. Odpowiedź brzmi: tak, ale należy zwrócić uwagę na ich parametry techniczne oraz wydajność, aby uniknąć problemów z działaniem systemu. Inna popularna kwestia dotyczy tego, jakie ciśnienie robocze powinno być ustawione dla połączonych kompresorów – zazwyczaj powinno być ono zgodne z wymaganiami narzędzi pneumatycznych używanych w danym miejscu pracy. Osoby planujące montaż często pytają także o to, jak długo trwa proces łączenia dwóch kompresorów – czas ten może się różnić w zależności od skomplikowania instalacji oraz doświadczenia osoby przeprowadzającej montaż.
Jakie są wskazówki dotyczące konserwacji połączonych kompresorów?
Aby zapewnić długotrwałe i efektywne działanie połączonych kompresorów, niezwykle istotna jest regularna konserwacja tych urządzeń. Przede wszystkim warto ustalić harmonogram przeglądów technicznych oraz konserwacji zgodny z zaleceniami producenta. Regularne sprawdzanie stanu technicznego urządzeń pozwoli na szybką identyfikację ewentualnych problemów oraz ich naprawę zanim staną się poważniejsze. Należy zwrócić szczególną uwagę na filtry powietrza oraz oleju – ich regularna wymiana jest kluczowa dla utrzymania wysokiej jakości sprężonego powietrza oraz wydajności pracy kompresora. Ważnym aspektem konserwacji jest także kontrola szczelności połączeń – wszelkie wycieki powietrza mogą prowadzić do obniżenia efektywności całego systemu i zwiększenia kosztów eksploatacyjnych. Oprócz tego warto monitorować poziom oleju w silniku oraz jego jakość – niewłaściwy olej lub jego niski poziom mogą prowadzić do uszkodzenia urządzenia.
Jakie są zastosowania połączonych kompresorów w różnych branżach?
Połączone kompresory znajdują szerokie zastosowanie w różnych branżach przemysłowych oraz usługowych dzięki swojej elastyczności i zwiększonej wydajności. W przemyśle budowlanym często wykorzystuje się je do zasilania narzędzi pneumatycznych takich jak młoty udarowe czy wiertarki, co pozwala na szybsze wykonywanie prac budowlanych i remontowych. W warsztatach samochodowych połączone kompresory służą do obsługi narzędzi takich jak klucze pneumatyczne czy podnośniki, co znacząco zwiększa efektywność pracy mechaników. W branży spożywczej i farmaceutycznej sprężone powietrze wykorzystywane jest do pakowania produktów oraz transportu materiałów w procesach produkcyjnych – tutaj szczególnie ważna jest jakość sprężonego powietrza wolnego od zanieczyszczeń olejowych. W przemyśle chemicznym połączone kompresory mogą być używane do kontrolowania procesów technologicznych wymagających precyzyjnego ciśnienia roboczego.