Fabryka przyszłości 4.0 to koncepcja, która odnosi się do nowoczesnych metod produkcji, wykorzystujących zaawansowane technologie cyfrowe oraz automatyzację. W dobie czwartej rewolucji przemysłowej, przedsiębiorstwa dążą do zwiększenia efektywności swoich procesów produkcyjnych poprzez integrację Internetu rzeczy, sztucznej inteligencji oraz analizy danych. W tym kontekście fabryki stają się bardziej elastyczne i zdolne do szybkiej adaptacji do zmieniających się warunków rynkowych. Kluczowym elementem fabryki 4.0 jest również zdalne monitorowanie procesów oraz możliwość ich optymalizacji w czasie rzeczywistym. Dzięki temu przedsiębiorstwa mogą lepiej zarządzać zasobami, minimalizować straty oraz poprawiać jakość produktów. Wprowadzenie tych innowacyjnych rozwiązań staje się nie tylko sposobem na zwiększenie konkurencyjności, ale także na zaspokojenie rosnących oczekiwań klientów, którzy coraz częściej poszukują produktów dostosowanych do ich indywidualnych potrzeb.
Jakie technologie są kluczowe dla Fabryki Przyszłości 4.0
W kontekście fabryki przyszłości 4.0 kluczowe są różnorodne technologie, które wspierają automatyzację i cyfryzację procesów produkcyjnych. Jednym z najważniejszych elementów jest Internet rzeczy (IoT), który umożliwia połączenie maszyn i urządzeń w sieć, co pozwala na zbieranie danych w czasie rzeczywistym oraz ich analizę. Kolejną istotną technologią jest sztuczna inteligencja (AI), która pozwala na podejmowanie decyzji opartych na analizie dużych zbiorów danych oraz przewidywanie awarii maszyn czy optymalizację procesów produkcyjnych. Robotyka również odgrywa kluczową rolę w fabrykach 4.0, gdzie roboty współpracujące (cobots) mogą pracować obok ludzi, zwiększając wydajność i bezpieczeństwo pracy. Dodatkowo technologie takie jak druk 3D umożliwiają szybkie prototypowanie i produkcję niestandardowych części, co znacznie skraca czas realizacji zamówień. Wreszcie, systemy chmurowe pozwalają na przechowywanie i przetwarzanie danych w sposób elastyczny i skalowalny, co jest niezbędne w dynamicznie zmieniającym się środowisku produkcyjnym.
Jakie korzyści przynosi wdrożenie Fabryki Przyszłości 4.0
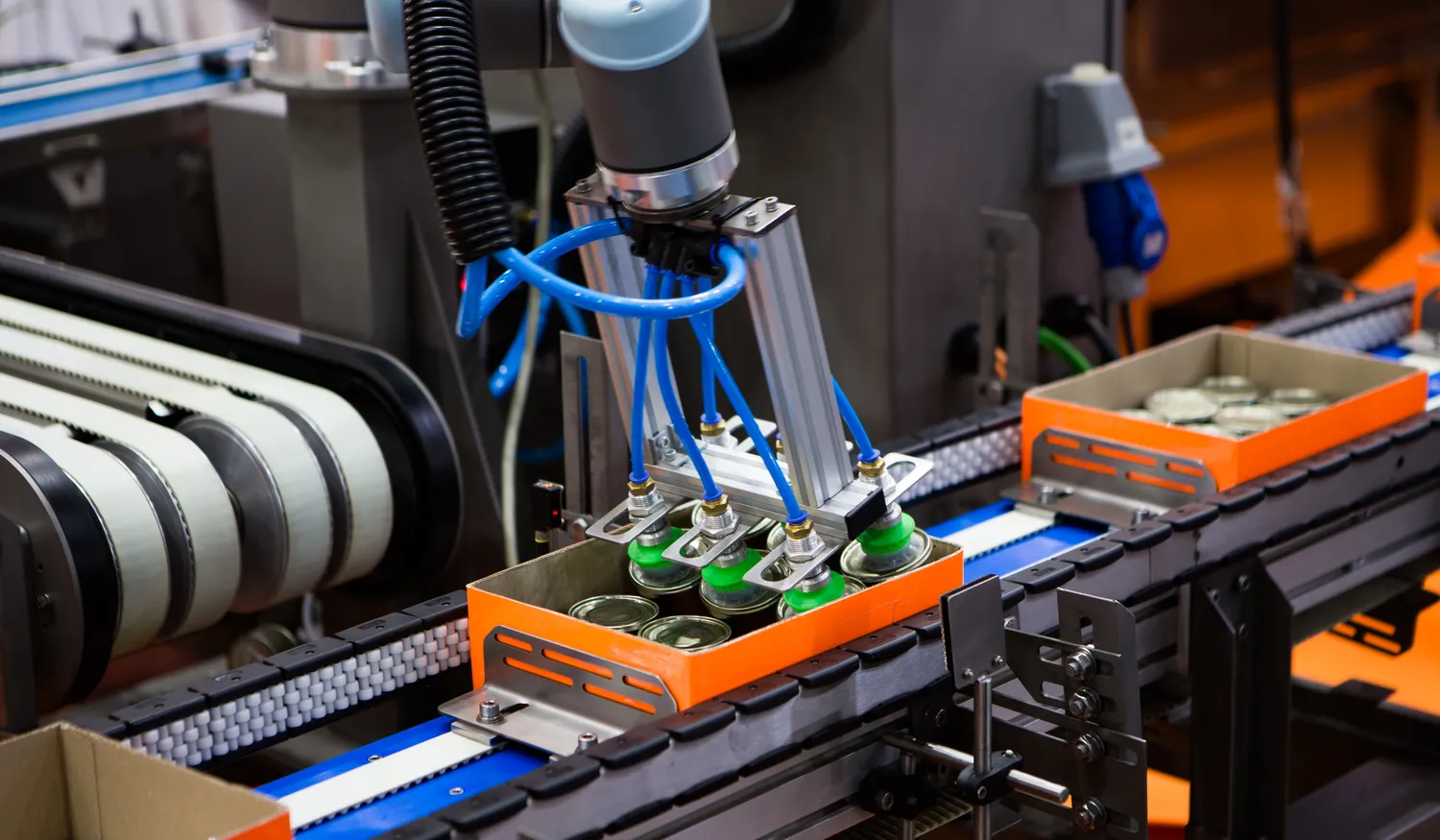
Wdrożenie koncepcji fabryki przyszłości 4.0 niesie ze sobą szereg korzyści dla przedsiębiorstw z różnych branż. Przede wszystkim dzięki automatyzacji procesów produkcyjnych można znacznie zwiększyć wydajność oraz obniżyć koszty operacyjne. Wykorzystanie zaawansowanych technologii pozwala na szybsze reagowanie na zmiany popytu oraz dostosowywanie produkcji do indywidualnych potrzeb klientów, co przekłada się na wyższą jakość obsługi klienta. Dodatkowo, dzięki zastosowaniu IoT i analityki danych możliwe jest lepsze monitorowanie stanu maszyn i urządzeń, co pozwala na przewidywanie awarii i minimalizowanie przestojów w produkcji. Warto również zauważyć, że fabryka 4.0 sprzyja zrównoważonemu rozwojowi poprzez efektywniejsze zarządzanie zasobami oraz redukcję odpadów produkcyjnych. Przemiany te wpływają również na poprawę warunków pracy pracowników, którzy mogą skupić się na bardziej kreatywnych zadaniach zamiast rutynowych czynności.
Jakie wyzwania stoją przed firmami przy wdrażaniu Fabryki Przyszłości 4.0
Wdrożenie koncepcji fabryki przyszłości 4.0 wiąże się z wieloma wyzwaniami, które przedsiębiorstwa muszą pokonać, aby skutecznie przeprowadzić transformację cyfrową swoich procesów produkcyjnych. Jednym z głównych problemów jest konieczność inwestycji w nowoczesne technologie oraz infrastrukturę IT, co może być kosztowne dla wielu firm, zwłaszcza tych mniejszych lub średnich. Ponadto wiele organizacji boryka się z brakiem odpowiednich kompetencji wśród pracowników, co utrudnia implementację nowych rozwiązań technologicznych oraz ich późniejsze wykorzystanie w codziennym funkcjonowaniu firmy. Również kwestie związane z bezpieczeństwem danych stają się coraz bardziej istotne w kontekście rosnącej liczby cyberataków oraz zagrożeń związanych z ochroną informacji przemysłowych. Dodatkowo firmy muszą zmierzyć się ze zmianami kulturowymi wewnątrz organizacji, które mogą być trudne do zaakceptowania przez pracowników przyzwyczajonych do tradycyjnych metod pracy.
Jakie przykłady zastosowania Fabryki Przyszłości 4.0 można znaleźć w branży
W różnych branżach można zaobserwować konkretne przykłady zastosowania koncepcji fabryki przyszłości 4.0, które ilustrują, jak nowoczesne technologie mogą zmieniać sposób produkcji i zarządzania. W przemyśle motoryzacyjnym wiele firm wdraża systemy automatyzacji, które pozwalają na zdalne monitorowanie linii produkcyjnych oraz optymalizację procesów w czasie rzeczywistym. Na przykład, znane marki samochodowe korzystają z robotów współpracujących, które wykonują precyzyjne zadania montażowe obok ludzi, co zwiększa wydajność i bezpieczeństwo pracy. W branży elektronicznej zastosowanie druku 3D pozwala na szybkie prototypowanie nowych produktów oraz produkcję niestandardowych komponentów, co znacząco skraca czas wprowadzenia produktu na rynek. Z kolei w sektorze spożywczym, firmy zaczynają wykorzystywać IoT do monitorowania jakości surowców oraz warunków przechowywania, co przyczynia się do poprawy bezpieczeństwa żywności. W przemyśle chemicznym natomiast, zaawansowane analizy danych pomagają w optymalizacji procesów produkcyjnych oraz redukcji odpadów.
Jakie umiejętności są potrzebne w erze Fabryki Przyszłości 4.0
W erze fabryki przyszłości 4.0 kluczowe staje się posiadanie odpowiednich umiejętności przez pracowników, aby mogli skutecznie funkcjonować w zautomatyzowanym i cyfrowym środowisku pracy. Przede wszystkim niezbędna jest znajomość technologii informacyjnych oraz umiejętność obsługi nowoczesnych narzędzi i oprogramowania, które wspierają procesy produkcyjne. Wiedza z zakresu analizy danych staje się coraz bardziej pożądana, ponieważ umożliwia podejmowanie decyzji opartych na faktach oraz przewidywanie trendów rynkowych. Również umiejętności związane z programowaniem i inżynierią systemów automatyki są niezwykle cenne w kontekście integracji różnych technologii w fabrykach 4.0. Ponadto, zdolności interpersonalne oraz umiejętność pracy zespołowej nabierają na znaczeniu, ponieważ współpraca między ludźmi a maszynami staje się kluczowym elementem efektywnego funkcjonowania nowoczesnych zakładów produkcyjnych.
Jakie są trendy rozwoju Fabryki Przyszłości 4.0 na świecie
Trendy rozwoju fabryki przyszłości 4.0 na świecie wskazują na rosnące zainteresowanie innowacjami technologicznymi oraz ich wpływem na przemysł. Jednym z najważniejszych kierunków jest dalsza automatyzacja procesów produkcyjnych poprzez wdrażanie robotów i systemów sztucznej inteligencji, które mogą wykonywać coraz bardziej skomplikowane zadania. Wiele firm inwestuje również w rozwój Internetu rzeczy (IoT), co pozwala na zbieranie danych z różnych urządzeń i ich analizę w czasie rzeczywistym, co przekłada się na lepsze zarządzanie zasobami oraz optymalizację produkcji. Kolejnym istotnym trendem jest wzrost znaczenia zrównoważonego rozwoju i ekologicznych rozwiązań w przemyśle, co skłania przedsiębiorstwa do poszukiwania sposobów na redukcję odpadów oraz minimalizację wpływu na środowisko naturalne. Warto także zauważyć rosnącą rolę chmury obliczeniowej, która umożliwia elastyczne przechowywanie danych oraz ich przetwarzanie bez konieczności inwestycji w kosztowną infrastrukturę IT. Wreszcie, rozwój technologii blockchain staje się coraz bardziej popularny jako sposób na zapewnienie transparentności i bezpieczeństwa transakcji w łańcuchu dostaw.
Jakie są perspektywy dla Fabryki Przyszłości 4.0 w Polsce
Perspektywy dla fabryki przyszłości 4.0 w Polsce są obiecujące, zwłaszcza biorąc pod uwagę dynamiczny rozwój sektora przemysłowego oraz rosnące zainteresowanie nowoczesnymi technologiami przez polskie przedsiębiorstwa. W ostatnich latach wiele firm zaczęło inwestować w automatyzację procesów produkcyjnych oraz cyfryzację swoich operacji, co przyczynia się do zwiększenia efektywności oraz konkurencyjności na rynku krajowym i międzynarodowym. Polska ma również silną bazę inżynieryjną oraz wykwalifikowaną kadrę specjalistów, co sprzyja wdrażaniu innowacyjnych rozwiązań technologicznych w przemyśle. Dodatkowo wsparcie ze strony rządu oraz funduszy unijnych dla projektów związanych z transformacją cyfrową stwarza korzystne warunki dla rozwoju fabryk przyszłości 4.0 w kraju. Warto jednak zauważyć, że przed polskimi przedsiębiorstwami stoją również wyzwania związane z koniecznością dostosowania strategii biznesowych do zmieniających się warunków rynkowych oraz potrzeb klientów. Kluczowe będzie także rozwijanie umiejętności pracowników oraz promowanie kultury innowacyjności wewnątrz organizacji.
Jakie są różnice między tradycyjnymi a nowoczesnymi modelami produkcji
Różnice między tradycyjnymi a nowoczesnymi modelami produkcji są znaczące i mają kluczowy wpływ na sposób funkcjonowania przedsiębiorstw w erze fabryki przyszłości 4.0. Tradycyjne modele produkcji często opierały się na liniowych procesach, gdzie każda faza była realizowana oddzielnie i niezależnie od innych etapów produkcji. Taki system charakteryzował się dużą ilością ręcznej pracy oraz ograniczoną elastycznością wobec zmian popytu czy wymagań klientów. Nowoczesne modele produkcji natomiast stawiają na integrację różnych technologii oraz automatyzację procesów, co pozwala na szybsze reagowanie na zmiany rynkowe i dostosowywanie produkcji do indywidualnych potrzeb klientów. W nowoczesnym podejściu kluczową rolę odgrywa analiza danych oraz wykorzystanie sztucznej inteligencji do optymalizacji procesów produkcyjnych i przewidywania trendów rynkowych. Ponadto nowoczesne modele promują współpracę między ludźmi a maszynami, co zwiększa efektywność pracy oraz bezpieczeństwo zatrudnionych osób.
Jakie są kluczowe elementy strategii wdrożenia Fabryki Przyszłości 4.0
Kluczowe elementy strategii wdrożenia fabryki przyszłości 4.0 obejmują kilka istotnych aspektów, które powinny być uwzględnione przez przedsiębiorstwa planujące transformację cyfrową swoich procesów produkcyjnych. Po pierwsze ważne jest przeprowadzenie dokładnej analizy obecnego stanu firmy oraz identyfikacja obszarów wymagających poprawy lub modernizacji. Następnie należy określić cele strategiczne związane z wdrożeniem nowych technologii i metod pracy, aby jasno określić kierunek działań firmy. Kolejnym krokiem jest wybór odpowiednich technologii i narzędzi informatycznych wspierających automatyzację i cyfryzację procesów produkcyjnych; powinny one być dostosowane do specyfiki działalności przedsiębiorstwa oraz jego potrzeb rynkowych.