Destylarka do rozpuszczalników to urządzenie, które umożliwia oddzielanie różnych substancji chemicznych na podstawie ich temperatury wrzenia. Proces ten jest kluczowy w wielu dziedzinach, takich jak przemysł chemiczny, farmaceutyczny czy kosmetyczny. W destylacji wykorzystuje się różnice w temperaturach wrzenia składników, co pozwala na ich skuteczne rozdzielenie. W praktyce, destylarka składa się z kilku podstawowych elementów, takich jak zbiornik na ciecz, kolumna destylacyjna oraz kondensator. Ciecz jest podgrzewana w zbiorniku, a pary unoszące się w górę przechodzą przez kolumnę, gdzie schładzają się i kondensują. W ten sposób można uzyskać czystsze frakcje rozpuszczalników. Ważne jest również odpowiednie ustawienie temperatury, aby maksymalnie wykorzystać efektywność procesu destylacji.
Jakie są zastosowania destylarki do rozpuszczalników
Destylarka do rozpuszczalników ma szerokie zastosowanie w różnych branżach przemysłowych oraz laboratoriach badawczych. W przemyśle chemicznym służy do oczyszczania surowców oraz odzyskiwania cennych substancji chemicznych z odpadów. Dzięki procesowi destylacji można uzyskać wysokiej czystości rozpuszczalniki, które są niezbędne w produkcji farb, lakierów czy tworzyw sztucznych. W laboratoriach badawczych destylarki wykorzystywane są do analizy składników chemicznych oraz przygotowywania próbek do dalszych badań. W przemyśle farmaceutycznym proces ten jest kluczowy dla produkcji leków, gdzie czystość substancji czynnych ma ogromne znaczenie dla skuteczności terapii. Ponadto, destylarki znajdują zastosowanie w produkcji kosmetyków, gdzie oczyszczone oleje i alkohole są używane jako składniki aktywne w różnych preparatach pielęgnacyjnych.
Jakie są rodzaje destylarek do rozpuszczalników
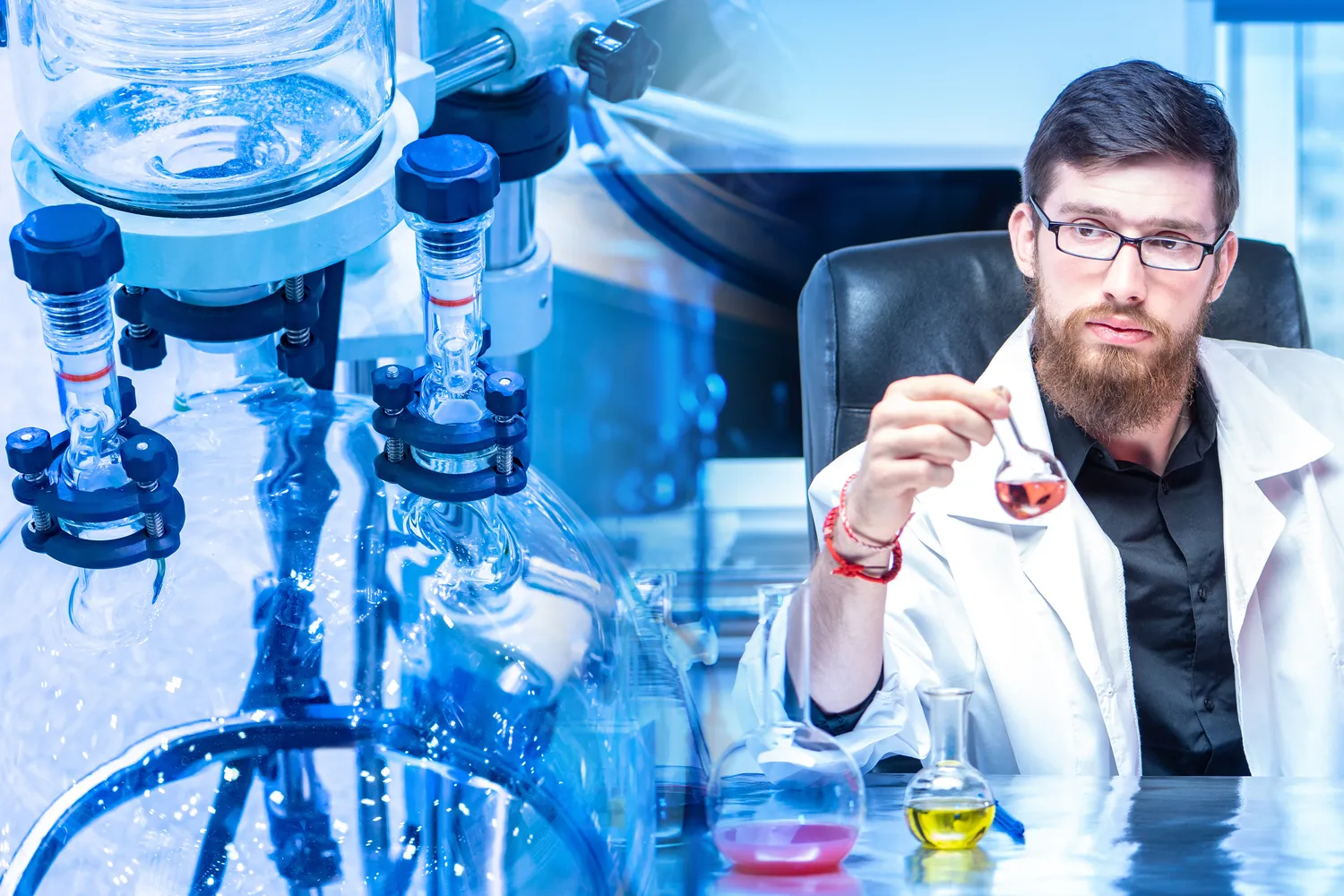
Na rynku dostępnych jest wiele rodzajów destylarek do rozpuszczalników, które różnią się konstrukcją oraz przeznaczeniem. Jednym z najpopularniejszych typów są destylarki prostoliniowe, które charakteryzują się prostą budową i łatwością obsługi. Są one idealne dla mniejszych laboratoriów oraz warsztatów rzemieślniczych. Innym rodzajem są destylarki frakcyjne, które umożliwiają jednoczesne oddzielanie kilku składników o różnych temperaturach wrzenia. Te urządzenia są bardziej skomplikowane i wymagają większej precyzji w ustawieniach temperatury oraz ciśnienia. W przypadku dużych zakładów przemysłowych często stosuje się destylarki z automatycznym sterowaniem procesem, co pozwala na zwiększenie efektywności produkcji oraz minimalizację błędów ludzkich. Warto również wspomnieć o nowoczesnych rozwiązaniach technologicznych, takich jak destylarki membranowe czy osmotyczne, które wykorzystują innowacyjne metody separacji substancji chemicznych.
Jakie materiały są używane do budowy destylarek
Budowa destylarki do rozpuszczalników wymaga zastosowania odpowiednich materiałów, które zapewniają trwałość oraz odporność na działanie chemikaliów. Najczęściej wykorzystywanym materiałem jest stal nierdzewna, która charakteryzuje się wysoką odpornością na korozję oraz łatwością w utrzymaniu czystości. Stal nierdzewna jest idealna do kontaktu z różnymi substancjami chemicznymi i nie wpływa na ich właściwości. W przypadku elementów narażonych na wysokie temperatury często stosuje się także materiały ceramiczne lub szkło borokrzemowe, które wytrzymują ekstremalne warunki bez ryzyka uszkodzeń. Ważnym aspektem jest również izolacja termiczna urządzenia, która może być wykonana z materiałów takich jak wełna mineralna czy pianka poliuretanowa. Izolacja ta zapobiega utracie ciepła podczas procesu destylacji i zwiększa efektywność energetyczną całego systemu.
Jakie są koszty zakupu i eksploatacji destylarki
Koszty zakupu i eksploatacji destylarki do rozpuszczalników mogą się znacznie różnić w zależności od jej typu, wielkości oraz przeznaczenia. Na rynku dostępne są zarówno proste modele laboratoryjne, których cena może wynosić kilka tysięcy złotych, jak i zaawansowane systemy przemysłowe kosztujące setki tysięcy złotych. Przy wyborze odpowiedniej destylarki warto zwrócić uwagę nie tylko na cenę zakupu, ale także na koszty eksploatacji związane z energią elektryczną potrzebną do podgrzewania cieczy oraz konserwacją urządzenia. Regularne przeglądy techniczne oraz wymiana zużytych części mogą generować dodatkowe wydatki. Istotnym elementem kosztowym jest także zakup surowców wykorzystywanych w procesie destylacji oraz ewentualne opłaty związane z utylizacją odpadów chemicznych powstałych podczas pracy urządzenia.
Jakie są najczęstsze problemy z destylarkami do rozpuszczalników
Podczas użytkowania destylarek do rozpuszczalników mogą wystąpić różne problemy, które mogą wpływać na efektywność procesu destylacji oraz jakość uzyskiwanych produktów. Jednym z najczęstszych problemów jest zatykanie się kolumny destylacyjnej, co może prowadzić do obniżenia wydajności urządzenia. Zatykanie to często spowodowane jest osadzaniem się zanieczyszczeń lub resztek chemicznych, które nie zostały usunięte przed rozpoczęciem procesu. W takich przypadkach konieczne jest regularne czyszczenie kolumny oraz innych elementów destylarki. Innym problemem może być niewłaściwe ustawienie temperatury, co skutkuje nieefektywnym oddzieleniem składników. Użytkownicy powinni zwracać uwagę na dokładność pomiaru temperatury oraz kalibrację urządzeń pomiarowych. Czasami zdarzają się również problemy z kondensatorem, który może nie działać prawidłowo, co prowadzi do utraty cennych substancji w postaci pary.
Jakie są zalety korzystania z destylarki do rozpuszczalników
Korzystanie z destylarki do rozpuszczalników niesie ze sobą wiele korzyści, zarówno w kontekście przemysłowym, jak i laboratoryjnym. Przede wszystkim, proces destylacji pozwala na uzyskanie wysokiej czystości substancji chemicznych, co jest niezwykle istotne w produkcji farmaceutyków oraz kosmetyków. Czyste rozpuszczalniki mają kluczowe znaczenie dla skuteczności końcowych produktów oraz ich bezpieczeństwa dla użytkowników. Dodatkowo, destylarka umożliwia odzyskiwanie cennych surowców z odpadów, co przyczynia się do zmniejszenia kosztów produkcji oraz ograniczenia negatywnego wpływu na środowisko. Kolejną zaletą jest możliwość dostosowania procesu destylacji do indywidualnych potrzeb użytkownika poprzez regulację temperatury i ciśnienia, co pozwala na optymalizację wydajności. Dzięki nowoczesnym technologiom, wiele destylarek wyposażonych jest w systemy automatycznego sterowania, co zwiększa komfort pracy oraz minimalizuje ryzyko błędów ludzkich.
Jakie są różnice między destylacją prostą a frakcyjną
Destylacja prosta i frakcyjna to dwa podstawowe rodzaje procesów stosowanych w destylacji rozpuszczalników, które różnią się zarówno metodą działania, jak i zastosowaniem. Destylacja prosta polega na podgrzewaniu cieczy do momentu jej wrzenia i zbieraniu pary, która następnie skrapla się w kondensatorze. Jest to metoda stosunkowo łatwa i szybka, idealna do oddzielania składników o znacznie różnych temperaturach wrzenia. Natomiast destylacja frakcyjna jest bardziej skomplikowanym procesem, który wykorzystuje kolumnę destylacyjną do separacji kilku składników jednocześnie. Dzięki zastosowaniu kolumny możliwe jest wielokrotne skraplanie i odparowywanie substancji, co pozwala na uzyskanie wyższej czystości poszczególnych frakcji. Destylacja frakcyjna jest szczególnie przydatna w przypadku mieszanin o zbliżonych temperaturach wrzenia, gdzie konieczne jest precyzyjne oddzielenie składników.
Jakie są najważniejsze parametry pracy destylarki
Aby zapewnić prawidłowe działanie destylarki do rozpuszczalników oraz uzyskać pożądane wyniki procesu destylacji, należy zwrócić uwagę na kilka kluczowych parametrów pracy urządzenia. Pierwszym z nich jest temperatura wrzenia cieczy, która ma bezpośredni wpływ na efektywność separacji składników. Użytkownik powinien monitorować temperaturę zarówno w zbiorniku, jak i w kolumnie destylacyjnej, aby uniknąć niepożądanych strat substancji czynnych. Kolejnym istotnym parametrem jest ciśnienie wewnętrzne w systemie; zmiany ciśnienia mogą wpłynąć na temperatury wrzenia substancji i tym samym na efektywność procesu. Również przepływ chłodziwa w kondensatorze ma znaczenie – odpowiednia regulacja tego parametru zapewnia skuteczne skraplanie pary i minimalizuje straty produktu. Oprócz tego ważne są także czas trwania procesu oraz ilość surowca poddawanego destylacji; te elementy powinny być dostosowane do specyfiki danego zadania technologicznego.
Jakie są wymagania dotyczące bezpieczeństwa przy użyciu destylarek
Bezpieczeństwo podczas użytkowania destylarek do rozpuszczalników jest niezwykle istotne ze względu na potencjalne zagrożenia związane z pracą z substancjami chemicznymi oraz wysokimi temperaturami. Przede wszystkim użytkownicy powinni przestrzegać zasad BHP oraz stosować odpowiednie środki ochrony osobistej, takie jak rękawice ochronne, gogle czy fartuchy laboratoryjne. Ważne jest także zapewnienie odpowiedniej wentylacji w pomieszczeniu, w którym znajduje się destylarka, aby uniknąć gromadzenia się szkodliwych oparów chemicznych. Należy również regularnie kontrolować stan techniczny urządzenia; wszelkie uszkodzenia czy nieszczelności mogą prowadzić do poważnych incydentów. Użytkownicy powinni być świadomi ryzyka pożaru lub eksplozji związanych z pracą z łatwopalnymi substancjami chemicznymi i stosować odpowiednie procedury awaryjne.
Jakie innowacje technologiczne dotyczące destylarek można zaobserwować
W ostatnich latach rynek technologii związanych z destylacją rozwija się dynamicznie, a innowacje technologiczne dotyczące destylarek do rozpuszczalników stają się coraz bardziej powszechne. Jednym z głównych trendów jest automatyzacja procesów produkcyjnych; nowoczesne urządzenia często wyposażone są w zaawansowane systemy sterowania komputerowego, które umożliwiają precyzyjne monitorowanie parametrów pracy oraz automatyczne dostosowywanie ustawień w czasie rzeczywistym. Dzięki temu można znacznie zwiększyć efektywność produkcji oraz jakość uzyskiwanych produktów. Kolejnym kierunkiem rozwoju są technologie związane z odzyskiem energii; nowoczesne systemy potrafią wykorzystywać ciepło odpadowe generowane podczas procesu destylacji do podgrzewania surowców lub innych mediów roboczych. Innowacyjne rozwiązania obejmują także zastosowanie materiałów kompozytowych czy nanotechnologii w budowie elementów urządzeń, co zwiększa ich trwałość oraz odporność na działanie agresywnych chemikaliów.